SUPPLY
CHAIN
AREA, STRATEGIC GOALS AND HIGHLIGHTS OF 2024Boundary 2 – Apatit, including its branches and standalone business units.
Target
9.1
- Further development of Process Mining and robotisation
- Development and implementation of new digital tools
- Five new robotiс solutions developed, two robotic solutions transferred to PIX Robotics, a new domestic platform, with changes in the logic.
- Procurement Workstation tool implemented, providing procurement managers with a work schedule for the near future that prioritises tasks.
- Methodology for calculating a standard workload unit for procurement managers developed and deployed using system objects.
Target
12.4
- Enhancing long‑term relationships with suppliers
- Developing direct and alternative supplies of imported equipment and spare parts
- Increased procurement using embossed bank cards
- Further development of category strategies
Target
8.3, 12.4,
13.2
- ESG evaluation coverage of at least 50% of counterparties that participated in the procurement and at least 50% of procurement volume from the evaluated counterparties
Training materials are available on the Company’s official website in the Procurement section
In 2024, PhosAgro Group won the Competitive Procurement Leader contest in the Unlocking Team Potential category.
Team development efforts at the Procurement Department of our subsidiary Apatit focus on hiring talent and providing support and encouragement to help employees achieve ambitious goals.
The Competitive Procurement Leader Award is the first professional competition in the field of trade and procurement, bringing together suppliers, government officials, mass media, and non‑governmental organisations. Established in 2012, the award aims to raise awareness about the most significant procurement projects that make operations of companies more efficient and contribute to the development of the market at large. In 2024, the competition saw 183 applications from Russia’s largest companies representing various industries.
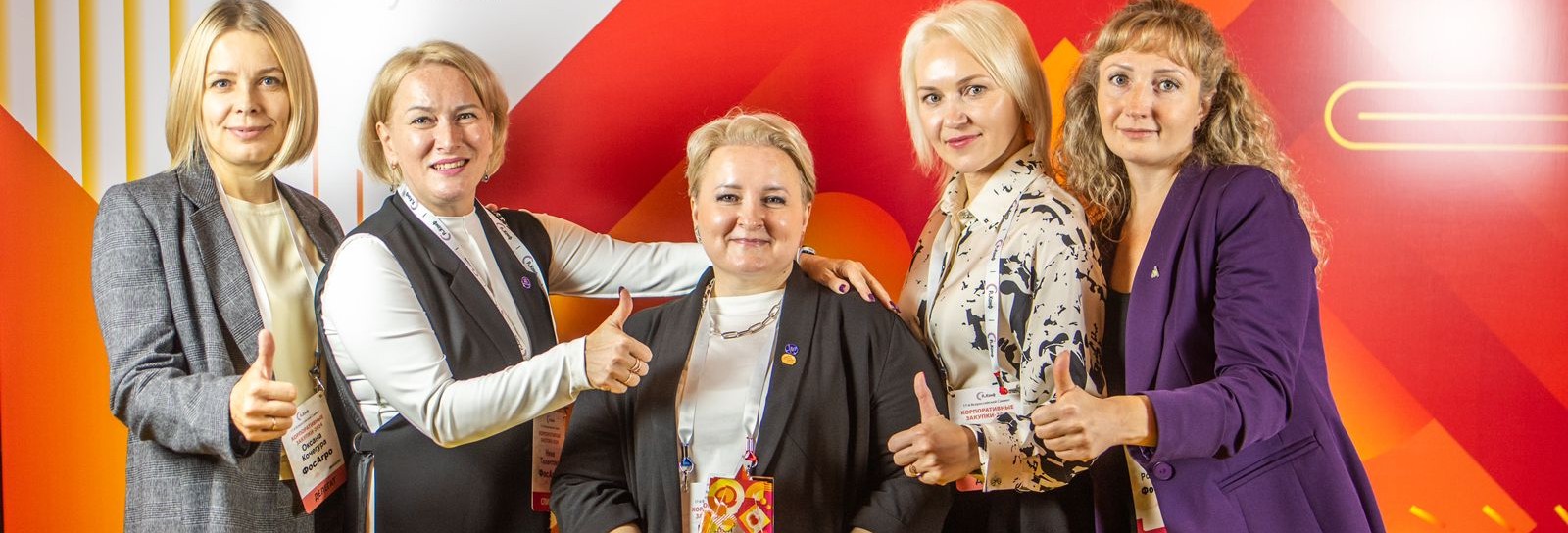
Oleg Minnullin Head of Procurement at ApatitThe key focus of 2024 was to keep up our momentum. We continued to implement the decisions made, looked for exciting new ideas, engaged in systemic analysis and enhancement of our business processes, and also went on fostering our corporate values in the team. Thanks to our targeted team efforts, we accomplished all our goals. We are looking forward to the launch of the project to transition to the new domestic ERP for procurement.
GRI 3‑3
PhosAgro’s procurement system seeks to ensure that the Group’s subsidiaries receive the required resources, materials, and services of adequate quality, in full and at reasonable prices. However, there is much more to the principles and business processes underlying our procurement activities. We believe that running a supply chain in an efficient and responsible manner is the cornerstone of the Company’s sustainable development.
Thousands of our suppliers and contractors benefit directly from these investments, and so do their employees, who have to provide for their families.
We contribute to the public budget at various levels. What is even more important is that the tools we use – such as our environmental and social assessments of suppliers, along with anti‑corruption mechanisms – directly promote values of sustainability and social responsibility across the Russian business community. These values are the bedrock of our business philosophy.
We work to ensure that our procurement activities have a strong positive impact on all our stakeholders.
GRI 3‑3
Our supply chain represents a set of interconnected processes covering all stages of value creation, from procurement to product delivery. The Group’s supply chain management focuses on ensuring the achievement of production targets via timely, complete, and high‑quality procurement, as well as boosting the Company’s efficiency.
Legitimate, competitive, and transparent procurement is among our key principles. In our relationships with competitors, we rely on mutual respect and avoid using unethical methods to gain a competitive advantage. The Company ensures compliance with Russian and other applicable anti‑monopoly laws in its operations.
Code of Conduct for Counterparties
PhosAgro Group’s Electronic Bidding Platform (EBP) Regulations
Strategy and Sustainable Development Committee of the Board of Directors
- Setting strategic priorities in procurement
- Review of the executive management’s procurement reporting
Director (Supervisor, officer‑in‑charge) of the Department
- Organising the overall operation, allocation of functions, business development strategies, definition of methodologies and procedures for the uninterrupted supply of equipment and materials
Department Director
Head of Division
- Meeting the Company’s needs in a timely manner
- Apatit’s warehouse inventory management
- Day‑to‑day functioning of the Department, supervising operations of the Department’s structural units
- Developing a strategy for re‑engineering of business processes in the Department, etc.
Heads of units and working groups
- Managing operations of subordinate business units, selecting and deploying staff
- Acting in accordance with the requirements of the management system, contributing to its improvement within their remit, etc.
Specialists
- Meeting the Company’s needs for equipment and materials, controlled materials, and services in a timely manner, in full and at the best possible prices
- Pursuing professional development and upskilling
KPIs are individual, and their calculation accounts for the personal contribution of each employee. Clear KPIs enable employees to understand what kind of performance is expected, and motivate them to work more productively. Ongoing monitoring of KPIs helps identify process vulnerabilities, make sound decisions while minimising risks, which results in higher effectiveness, better performance, and enhanced procurement strategy.
Continuous business process development and improvement underpins successful operation of the Company on the whole and of the Procurement Department in particular. We never stop learning and adopting best practices. PhosAgro Group strives to use modern tools to boost its business efficiency and ensure maximum transparency of its key processes.
The Group’s potential suppliers can participate in a fully transparent and accessible procurement procedure using the Company’s electronic bidding platform.
The Group’s potential suppliers can participate in a fully transparent and accessible procurement procedure using the Company’s electronic bidding platform.
Committed to fighting corruption, the Company adheres to the Anti‑Corruption Charter of the Russian Business. At PhosAgro Group, we establish and maintain business relationships with partners that operate in a bona fide manner, care about their own reputation, show commitment to high ethical standards, combat corruption, and take part in joint anti‑corruption initiatives in accordance with Article 13.3 of the Federal Law On Combating Corruption.
The Company expects its counterparties to report in good faith any concerns related to its activities.
As a way to ensure prompt response to suspected corruption and fraud, in 2016, PhosAgro launched a Group‑wide hotline for the management to better handle all reports of violations and issues, including those related to procurement. PhosAgro Group’s hotline is available to everyone, including the Company’s contractors and partners.
The hotline regulations can be found here.
For more information on the Company’s relationships with local and SME suppliers, see Procurement function development in this section.
The following strategic risks affect our procurement objectives:
corruption risk
commodity risk
sanctions risk
Suppliers’ failure to perform, changes in the product range or late delivery of materials and equipment, including as a result of geopolitical factors
Violations of ESG principles by suppliers, including breach of human rights, use of child and forced labour, non‑compliance of products with environmental standards, etc.
Quality of raw materials, commodities, and equipment, dissatisfaction of the internal customer
The Group develops corrective measures as necessary and unlocks opportunities to mitigate those risks. Below you can find more information about what we do on this front, including:
implementation of digital procurement tools;
development of relationships with domestic manufacturers and ensuring alternative supplies of imported equipment and spare parts;
enhancement of the procurement efficiency and the quality of procured materials and equipment through building up the procurement function and assessing suppliers.
For more information, see the Strategic Risks section
In 2024, the Company was actively working to develop and implement digital tools in various procurement areas.
The Process Mining smart platform helped:
- develop new dashboards to analyse procurement categories, including a dashboard with a ready‑to‑use ABC analysis tool;
- implement a system for automated calculation of EBP bidding economic effect.
The Procurement Workstation tool was implemented to help procurement managers streamline their daily routines. The system automatically generates a schedule for all items to be processed in accordance with prescribed timelines.
To address the lack of a workload assessment tool for procurement managers,all items handled by procurement managers were digitalised, with work complexity quantified. This data was then used to develop a methodology for calculating a standard workload unit for procurement managers:
- the standard workload unit is calculated using a BI report sourced from the in‑house ERP;
- all necessary data is represented and visualised in an Excel dashboard;
- data updating is configured through exporting and using Power Query.
To ensure comprehensive end‑to‑end recording of breaches lacking systemic records in the in‑house ERP, new events related to supplier breaches of contractual obligations were added to the Occurrences and Events Record Book module based on the WSS Docs EDMS in 2024.
Bitrix24 was introduced to create a single system for task management and control within the Procurement Department.
An index and rating model of the automatic counterparty assessment was integrated into the SCOUT system, providing a comprehensive view of counterparties based on data from both PhosAgro Group’s internal and external sources.
New robotic solutions were developed and implemented for tasks such as downloading reports, searching for prices in pricing records, updating delivery schedules, etc.
PhosAgro Group places special emphasis on strengthening its supply chain in response to global geopolitical tensions. Adaptation to new technologies, changes in trade policies, and tightening sustainability requirements are presenting both new challenges for the Company.
We continued closer and more efficient collaboration with Russian manufacturers, with a variety of trials held and agreements signed for long‑term cooperation and fine‑tuning of equipment (including sludge pumps, filter materials, circulators and mixers, spare parts for main process equipment, self‑propelled underground machinery, and automation and control equipment) to meet the needs of Apatit.
Procurement highlights in 2024
KPI | Performance level | Actual | ||
---|---|---|---|---|
Threshold | Target | Stretch | 2024 | |
Average number of tender participants in the reporting period | 3 | 5 | 7 | 5 |
Tender price reduction in the reporting period, % | 20 | 30 | 35 | 32 |
Holding tenders on time, % | 90 | 95 | 100 | 99 |
KPI | Performance level | Actual | ||
---|---|---|---|---|
Threshold | Target | Stretch | 2024 | |
Timeliness of procurement (integrated) | 87 | 90 | 93 | 97 |
Reject rate at incoming control | 5 | 3 | 2 | 4 |
KPI | Performance level | Actual | ||
---|---|---|---|---|
Threshold | Target | Stretch | 2024 | |
Raw materials procurement index | 1.05 | 1 | 0.95 | 1 |
Performance improvement
In 2024, PhosAgro Group successfully completed the initiative to update its stock item catalogue, which resulted in several key improvements:
- the procurement category structure was aligned with the needs of the procurement process participants;
- catalogue attributes within the system, including adjusted procurement categories, were updated;
- duplicate items were removed.
Local supplier management
GRI 204‑1
PhosAgro Group is actively engages in projects aimed at supporting local suppliers and developing SMEs.
The Company is participating in the Synergy of Growth project in the Vologda region, which seeks to enhance the industrial potential of the region by increasing the share of the large businesses’ procurement from local SMEs. The Synergy of Growth 3.0 project employs a cluster model to advance the Vologda region’s economy and builds upon the Synergy of Growth initiative. It establishes a new mode of partnership between SMEs and industrial giants, focusing on joint development of required products.
MED 8, 9
2022 | 2023 | 2024 | |
---|---|---|---|
SMEs | 42,143.22 | 57,957.23 | 65,095.13 |
Local | 37,099.57 | 41,493.65 | 49,801.90 |
Imports | 5,914.77 | 12,436.83 | 10,140.55 |
PhosAgro is also collaborating with local enterprises by organising Supplier Days and taking part in forums and other initiatives run by the Urban Development Agency in Cherepovets as well as the regional office of the Russian Union of Industrialists and Entrepreneurs in the Vologda region (e.g. VII International Industrial Forum).
In May 2024, an offline meeting was held between representatives of SMEs in Cherepovets and Apatit employees. The meeting was also live‑streamed for the general public. A total of 77 representatives of local suppliers and contractors attended the event, while the additional 677 participants joined online. Such hybrid meetings enhance collaborative processes, expand cooperation opportunities, and foster effective win‑win partnerships, allowing each party to identify the best work strategies for themselves and their partners. The participants received a tutorial deck covering the matters discussed during the meeting.
PhosAgro Group is actively introducing sustainability principles across its operations. The Company has an automated system in place to evaluate suppliers on the basis of ESG criteria, which results in an individual rating of each counterparty. This enables us to assess our suppliers’ environmental, social, and governance performance paying special attention to supplier engagement. To ensure reliability and predictability of cooperation, the Company runs technical supplier audits, including requirements as to their environmental and social footprint. In 2024, we held 58 technical audits of Russian manufacturers, resulting in partnerships with six of them ultimately declined.
PhosAgro Group’s suppliers play an important role in advancing the Company’s sustainability strategy, helping foster a more eco‑friendly, socially responsible, and economically stable future.
In 2024, PhosAgro Group, as part of the National ESG Alliance, contributed to developing methodological recommendations for ESG evaluation of suppliers. These recommendations include several ESG checklists: a basic checklist with 28 questions, an advanced checklist, and a market leader checklist. The proposed checklists can be used by any company regardless of their expertise in sustainable procurement.
For more information about the project, visit the website
Key ESG evaluation indicators
Item | 2022 | 2023 | 2024 |
---|---|---|---|
Number of counterparties that participated in the evaluation on PhosAgro’s EBP as at the end of the reporting period | 7,605 | 11,191 | 14,885 |
Number of suppliers in the reporting year | 3,511 | 3,797 | 3,968 |
Number of rated suppliers in the reporting year | 1,888 | 2,418 | 2,685 |
Share of rated suppliers in the reporting year, % | 54 | 64 | 68 |
Total supplies, RUB bln | 213.9 | 183.8 | 216.7 |
Supplies from rated counterparties in the total volume of supplies in the reporting year, RUB bln | 74.8 | 108 | 137 |
Share of supplies from rated counterparties in the total volume of supplies in the reporting year, % | 35 | 59 | 63 |
Average supplier rating, % | 62 | 65 | 65 |
Supplier environmental assessment
GRI 308‑1, 308‑2
Environmental standards observed by PhosAgro Group’s suppliers include the use of environmentally sound technologies, reduction of GHG emissions, and sustainable use of natural resources. This approach helps minimise a environmental footprint and maintain ecosystems. In 2024, suppliers with an environmental management system certified to ISO 14001 or a similar standard represented 34% of the rated producers of raw materials, fuel, energy, and commodities, while the overall number of suppliers went up year‑on‑year.
Item | 2022 | 2023 | 2024 |
---|---|---|---|
Total number of rated suppliers | 1,888 | 2,418 | 2,685 |
Number of rated suppliers producing raw materials, fuel, energy, and commodities | 847 | 908 | 949 |
Number of rated suppliers producing raw materials, fuel, energy, and commodities with an environmental management system certified to ISO 14001 or a similar standard | 276 | 310 | 322 |
Share of rated suppliers producing raw materials, fuel, energy, and commodities with an environmental management system certified to ISO 14001 or a similar standard, % | 33 | 34 | 34 |
Supplier social assessment
GRI 414‑1, 414‑2
The social assessment of the Company’s suppliers takes into account such factors as working conditions, human rights, and corporate social responsibility. The analysis of changes in ESG evaluation items shows that most of the Group’s partner companies seek to operate in compliance with the labour laws and recognised safety standards.
Item | 2022 | 2023 | 2024 |
---|---|---|---|
Total number of rated suppliers | 1,888 | 2,418 | 2,685 |
Number of rated suppliers that adopted a zero‑tolerance policy on child labour | 1,091 | 1,511 | 1,715 |
Share of rated suppliers that adopted a zero‑tolerance policy on child labour, % | 58 | 62 | 64 |
Number of rated suppliers in the categories “Producers of raw materials, fuel, energy”, “Commodity producers and intermediaries”; “Logistics services”; “Construction and installation, repairs” | 1,524 | 1,926 | 2,129 |
Number of rated suppliers in the above categories that adopted a zero‑tolerance policy on discrimination | 831 | 1,151 | 1,294 |
Share of rated suppliers in the above categories that adopted a zero‑tolerance policy on discrimination, % | 55 | 60 | 61 |
Number of rated suppliers in the above categories that adopted a zero‑tolerance policy on forced labour | 856 | 1,171 | 1,313 |
Share of rated suppliers in the above categories that adopted a zero‑tolerance policy on forced labour, % | 56 | 61 | 62 |
Number of rated suppliers in the categories “Producers of raw materials, fuel, energy, and commodities”, “Logistics services; construction and installation, repairs” | 1,174 | 1,303 | 1,362 |
Number of rated suppliers in the above categories with an occupational health and safety management system certified to OHSAS 18001 or a similar standard | 452 | 518 | 542 |
Share of rated suppliers in the above categories with an occupational health and safety management system certified to OHSAS 18001 or a similar standard, % | 39 | 40 | 40 |